We’re well underway
The UNITED GRINDING Group’s IMPACT 4530 is the world’s first ‘Made in Switzerland’, industrial format additive machine tool. In an interview with Professor Markus Bambach from ETH Zurich, CEO Stephan Nell explains the potential of the new technology.
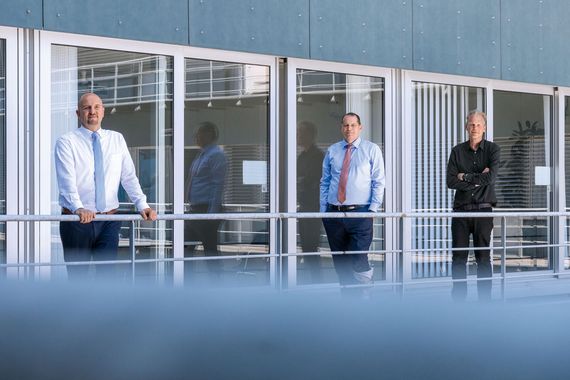
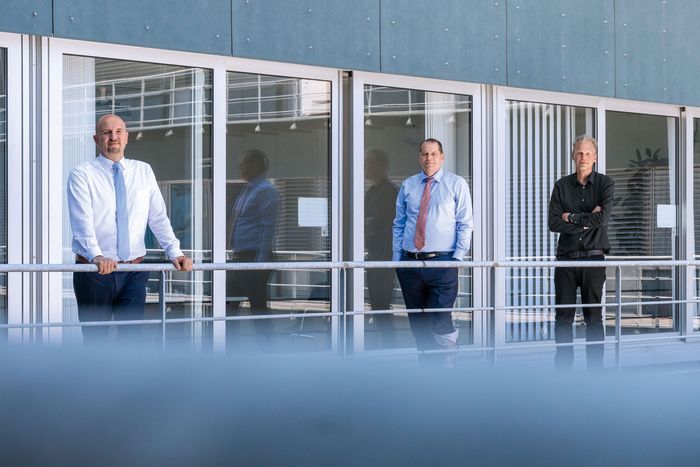
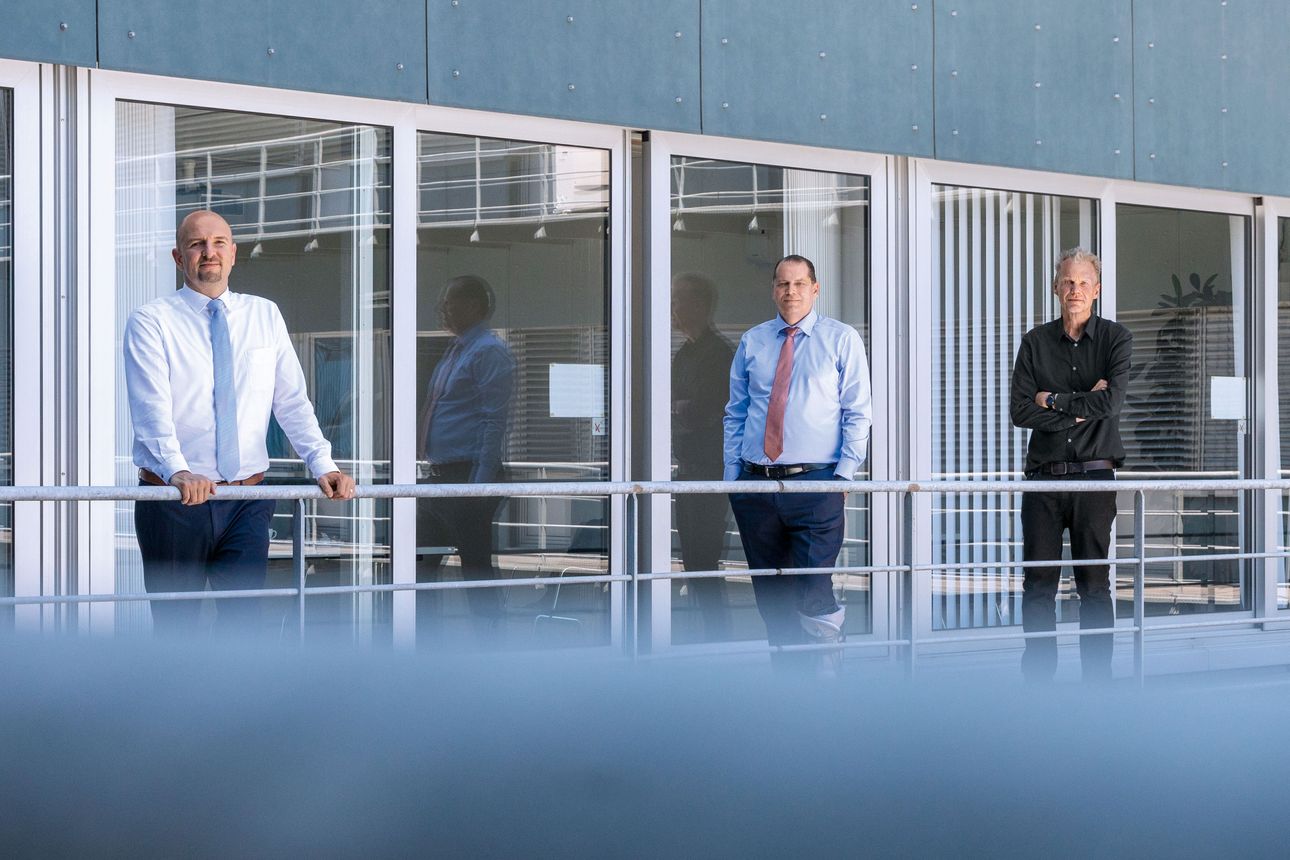
Mr. Nell, does the UNITED GRINDING Group with the IMPACT 4530 strive to become the technology leader in machine tools for additive manufacturing?
Stephan Nell: We certainly want to be at the forefront. There are many established manufacturers with years of experience with additive manufacturing and a solid track record. But we wanted to bring our own DNA to the topic, and this includes high reliability and availability. Our focus is always on making our customers successful. By offering the best technology available.
What's the strategic value of this area?
Stephan Nell: Additive manufacturing can be one manufacturing stage prior to grinding, and it goes to certain consumer industries that represent potential customers for 3D printing. And it is, of course, a new manufacturing field that requires a lot of innovation. After all, grinding has been around forever, it's fair to say. The only way forward is evolutionary. Of course, new innovations are constantly being added and the machines are getting better and better. But there are no new giant steps. By contrast, 3D printing is a fundamentally new technology. And that caught our attention
Mr. Bambach, can we already say with certainty today that additive manufacturing represents a real technological leap?
Markus Bambach: Yes, I certainly think we are dealing with a technological leap here. If you think back to the first industrial revolution, where the loom was invented and later made programmable with a punched card, you can find many examples over time when hardware and software innovation went hand in hand to create a technological leap. Additive manufacturing needs be no different – we must have a good machine on the hardware side, while also mastering the entire chain on the software side.
Mr. Nell, how exactly did you enter into this new field of technology, because it's not that kind of thing you can simply decide to do overnight.
Stephan Nell: Yes, it was a bit of a journey. We started by imagining ourselves in the role of the customer to such a machine manufacturer. This is what we did with Inspire — who have experience with 3D printing since 1996, and we subsequently gained access to this network directly with the purchase of IRPD. And then we let the development team and the Inspire people with previous 3D experience come together with the instructions: Do your thing. The result is the IMPACT 4530 – 9.2 tons of Swiss mechanical engineering.
Mr. Bambach, is the UNITED GRINDING Group simply following the textbook here?
Markus Bambach: No doubt, there are some unique selling points for additive manufacturing. For example, cost per component can be made more independent of the complexity of the components and the number of units. That’s not the case with other procedures. In addition, production can be handed locally, in a decentralized fashion. Nevertheless, one must always think about the cost structure in production chains. And if the cost question is dominant, then you can't make the case commercially for additive manufacturing as we know it today. Because it often takes a relatively long time and requires a lot of experience before a component can be printed at all. For more complex components and more difficult applications, you’ll need to hire a team of engineers and let them work for several weeks before you actually have a component that meets the requirements. But UNITED GRINDING now has a very solid machine on the market — on a market in which it is already established. These are very good prerequisites.
Mr. Nell, Mr. Bambach still seems to be waiting for the technology to keep advancing
Stephan Nell: We never believed that additive manufacturing should replace grinding. On the one hand, the process does not offer the same surface quality. Nor can it match its precision. But it does provide us with a new generative process upstream of the grinding machines that can enhance their abilities. It is one of many technologies that complements our existing portfolio well. If you look at a MÄGERLE machine tool today, it can not only grind, but also mill and drill. It is a machining center. At WALTER EWAG, we developed laser technology. Many people don't even know that we produce more measuring machines than some of the leading specialists in that technology. Additive machine tools also fit into this concept.
In conversation with the young engineers at IRPD in St. Gallen, the idea was that additive manufacturing would give us better products overall. Where do you see the boundaries of this utopia?
Stephan Nell: Here’s what the engineers got right: 3D production can open up completely new possibilities for designers. Firstly, they have to learn to design a part in such a way that they can take the advantages of 3D printing. There is no point in moving an existing part that is being made today on a milling machine or lathe one-to-one to a 3D printer.
Markus Bambach: If you were to sell a 3D machine to a service provider who earns money in the machining sector, without a designer — it’s unlikely you’d end up with better parts. After all, they're still thinking in terms of a design to be manufactured by machining. The successful examples I’m aware of come mainly come from the hydraulics sector. Or cooling, where integral parts can be printed instead of producing many individual parts. These examples each show a technological leap in which the potential is systematically increased. For example, in the aerospace industry, where extreme lightweight construction is possible. Then we can look at medical technology, where individualized components are important. But it’s a little too much for me to say right now that the technology inherently means better products for society. The largest 3D series production I know is a couple of tens of thousands of designer spectacles per year. It’s just not possible to produce two million parts – the technology has its limits.
Stephan Nell: There are limits, of course. But at the same time, we can observe progress underway. To this point, most 3D printers have been used in the metallurgy departments at universities and in testing departments of companies. But now customers want to use the machines for industrial production and are not interested in optimizing processes. They want it to work. And that’s what the IMPACT 4530 does.
What exactly are customers’ requirements for an industrial-grade 3D printing machine tool?
Stephan Nell: It must run stably, work quickly, and not make any mistakes. This is why the IMPACT has up to four lasers with 1,000 watts each. They do however naturally leave traces of smoke residue, which must be dealt with. Then there are seemingly simple things: We monitor the lip that coats the material, and replace it automatically if a defect is detected to prevent it from continuing to operate improperly. And then it is also important, at an industrial process level, that the customer does not have to constantly monitor the machine with personnel, which costs money. It must therefore have a high level of autonomy and largely be able to monitor itself. Generally speaking, parts and material change, and the machine needs to be able to deal with that. I cannot lose one or two shifts just to change materials. We take just 120 minutes to change materials, and it takes 15 minutes from job to job. In addition, we have many customers who mill, turn, grind, who have many production technologies in-house with a correspondingly high headcount. They’ll need to integrate 3D printing accordingly. So I need to design the machine in such a way that there is no contamination of the environment. Because people must not come into direct contact with the metal powder.
That sounds like the right way to go. Perhaps this utopia is attainable, Mr. Bambach?
Markus Bambach: Perhaps, presuming additive manufacturing continues to evolve as a technology. But I don't yet view it as being a substitute for established mass production-capable technologies, so to speak. Ongoing development of the software solutions is also important.
Stephan Nell: I think it’s great to orient oneself towards Utopian ideas. And the IRPD team in St. Gallen is hard at work optimizing the software solutions. In the end, it is an efficiency question for most customers. Ecological aspects also play a major role here. Additive manufacturing has a lot of potential in this area. There’s less need for transportation, and supply chains can be shortened. I am convinced that additive manufacturing will find its way into the machine tool industry. But it will not displace or replace everything else.
Taking part in the discussion
Text: Michael Hopp, Photography: Thomas Eugster