The miracle from St. Gallen
With its IMPACT 4530, the UNITED GRINDING Group has developed the world’s first “Made in Switzerland” additive machine tool for industrial use— from the small town of St. Gallen. How was this success achieved?
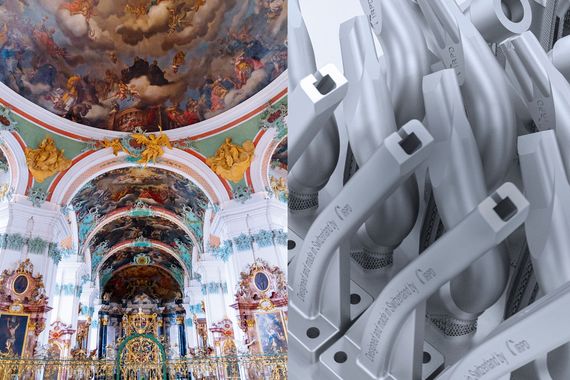
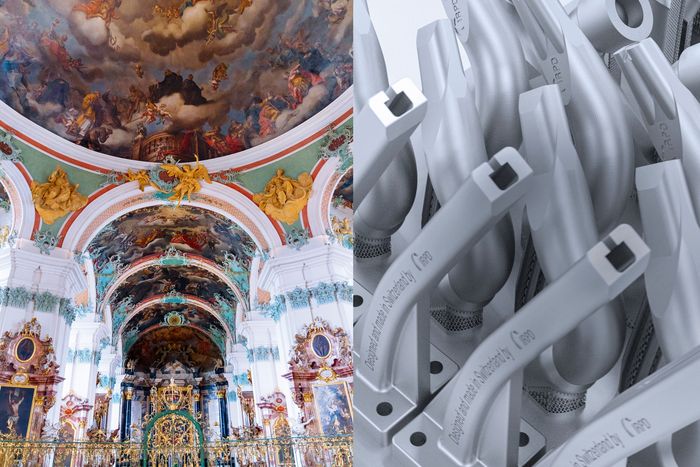
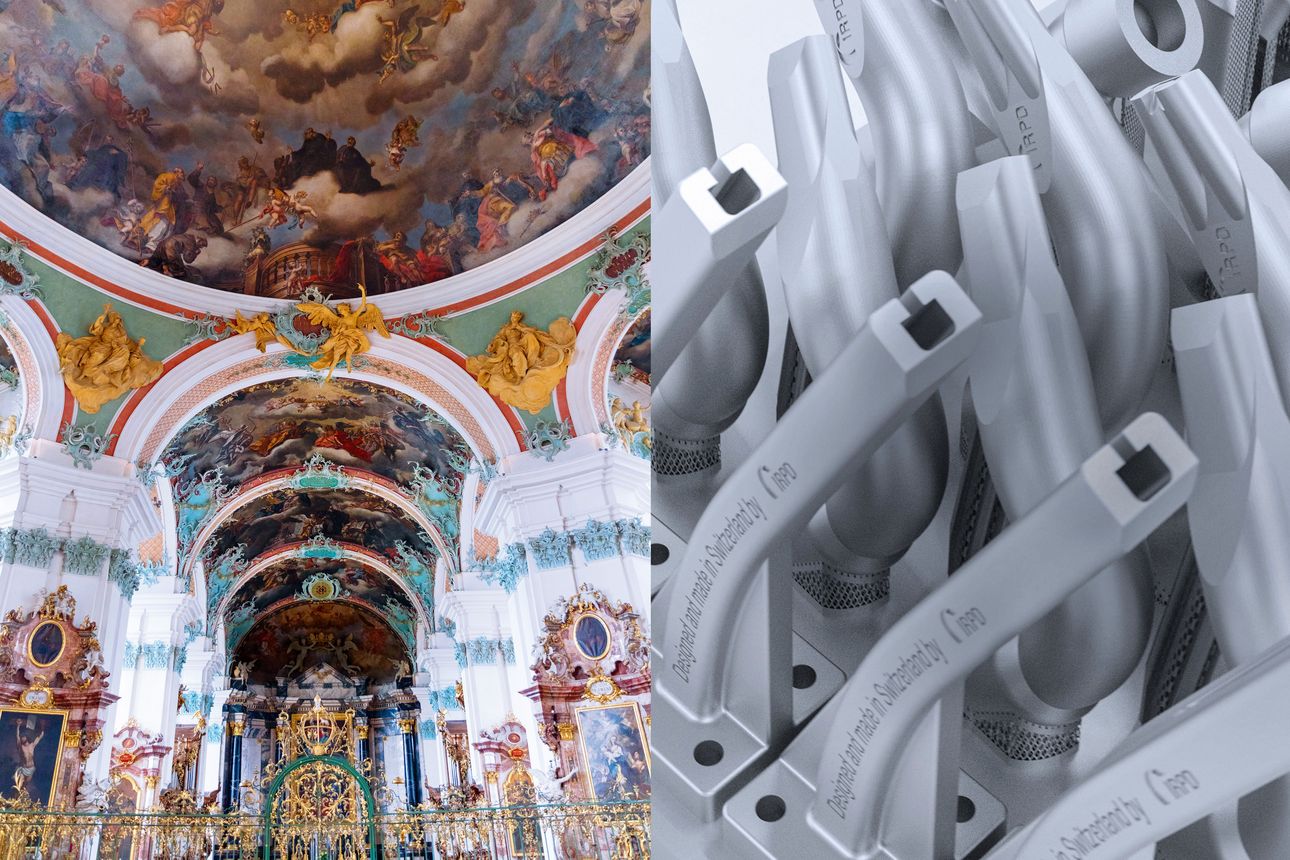
THE CLEAN NEW TURNKEY IMPACT 4530 stands in a room at the St. Gallen IRPD R&D center that was built especially for it. Its reputation already far proceeds it: the world's first industry-ready machine for additive manufacturing. There's no grinding of workpieces in this case; “manufacturing” in this case is actually precisely the opposite process. “Unlike classical production technology, where material is removed from a solid block by machining,” explains Paul Kössl, Head of Business Development and Marketing of UNITED GRINDING Group, “metal powder is used to build up a component additively, bit by bit as a layer beam melts it layer by layer (LPBF process).” The “face” of the IMPACT 4530 is an almost human-sized 54-inch touchscreen display in a friendly and intuitive design. This human-machine interface transmits the live images of the micro-welding process from a camera installed in the installation space and combines them with control elements and information on the process sequence. UNITED GRINDING Digital Solutions™ transfers data to the C.O.R.E. operating system. “It was a priority for us to integrate the IMPACT 4530 into the highly automated system network in a user-friendly way, enabling efficient networking with other machine tools,” says Köss
The dance of the laser
The IMPACT 4530 consists of two separate decoupled machine units. The thermostabilized, vacuum-capable machine core built on a cast-iron machine stand, the construction space, and the supply unit designed as a welding construction are successfully implemented as a separate operating and loading area. Together with the integrated automatic changeover system for the gas-tight metal powder containers and the components, this ensures the machine operable never comes into contact with the metal powder. While the IMPACT 4530 goes about its work, the screen shows the lasers dancing like four yellow flames, building circles, lines, corners, and edges atop a layer of the metal powder. This process is called selective laser melting of metal powders in the LPBF process (Laser Power Bed Fusion), which it handles with two or four 1000-watt industrial fiber lasers.
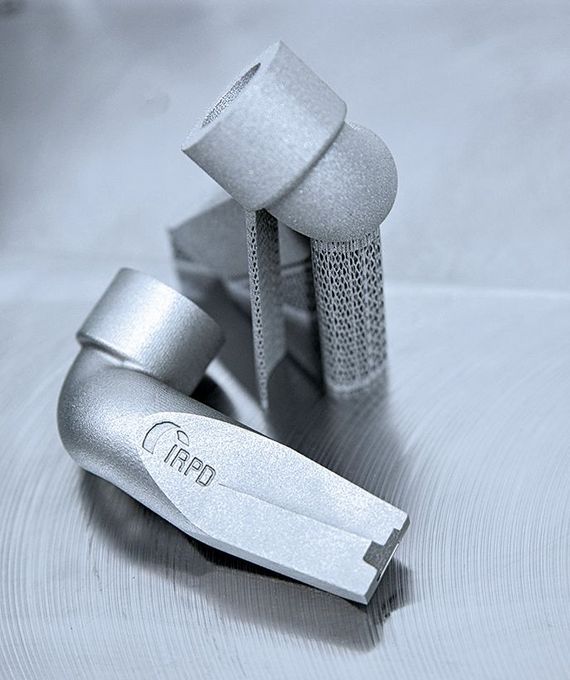
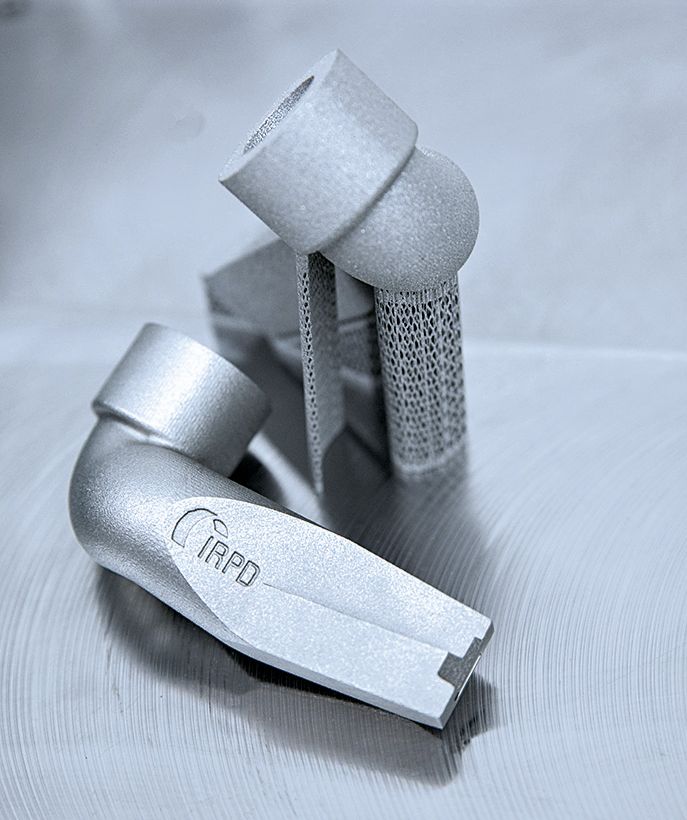
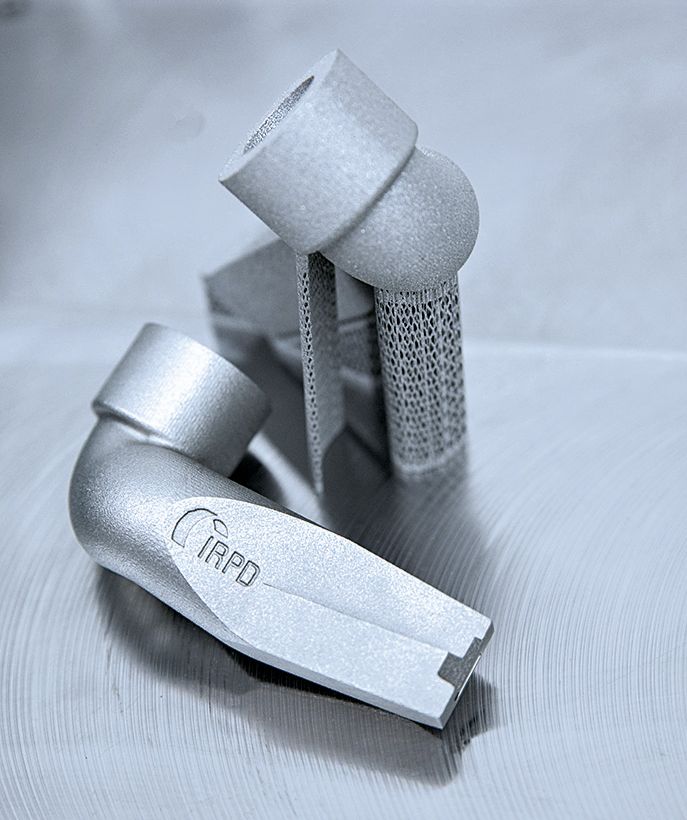
Ideas immediately become reality
The metal components are ultimately welded together layer by layer on the plate. The metal powders are offered in different grades and in steel, aluminum, titanium and nickel-based alloys as well as special metals — the right selection and mixing is crucial for the quality of the products. One of the greatest advantages of 3D printing is that new, creative ideas can be implemented quickly and at low cost, says Michael Schneider, head of additive services & customer care at IRPD. “This inherently leads to better components and thus to better products.” Alongside Pascal Brunner, Kai Gutknecht, and Alex Frauchiger, Schneider is one of the experts who has been closely involved in the development of the IMPACT 4530 since 2016. Schneider explains creating workpieces seemingly out of nothing requires only the CAD 3D data of the desired component, which the printer uses to calculate the various layers. For example, the movement plan for the deflection of the laser is created by a mirror system, which melts the individual layers at specific points, thus fabricating the component. “The 3D printing process allows for components to be created that would not be possible at all using classic machining,” says Alex Frauchiger, who is responsible for process and material development. This is perhaps the most important principle in the use of additive manufacturing. It is not a question of replicating the classic process, but rather rethinking the components themselves and thus realizing the added value of additive manufacturing. “It always starts with the analysis of where additive manufacturing actually adds value,” he explains. This might involve faster production, new functions, or a combination of features.
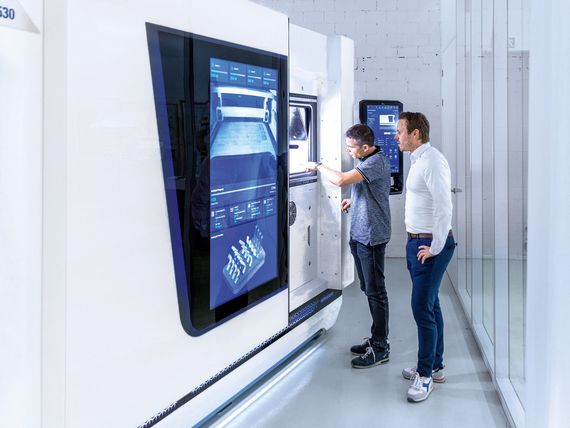
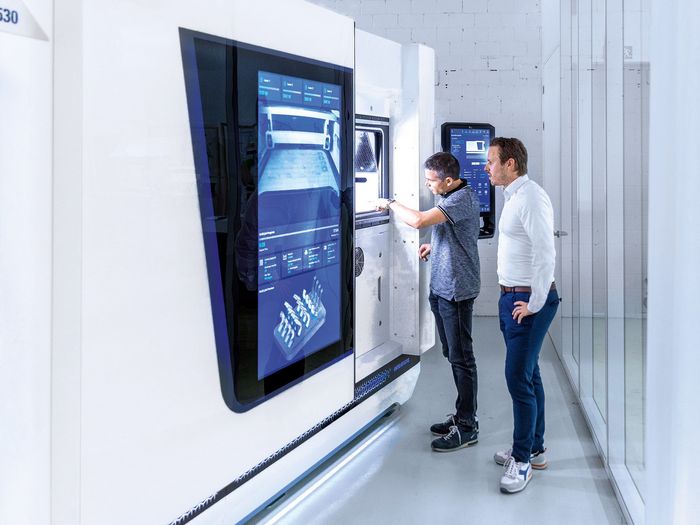
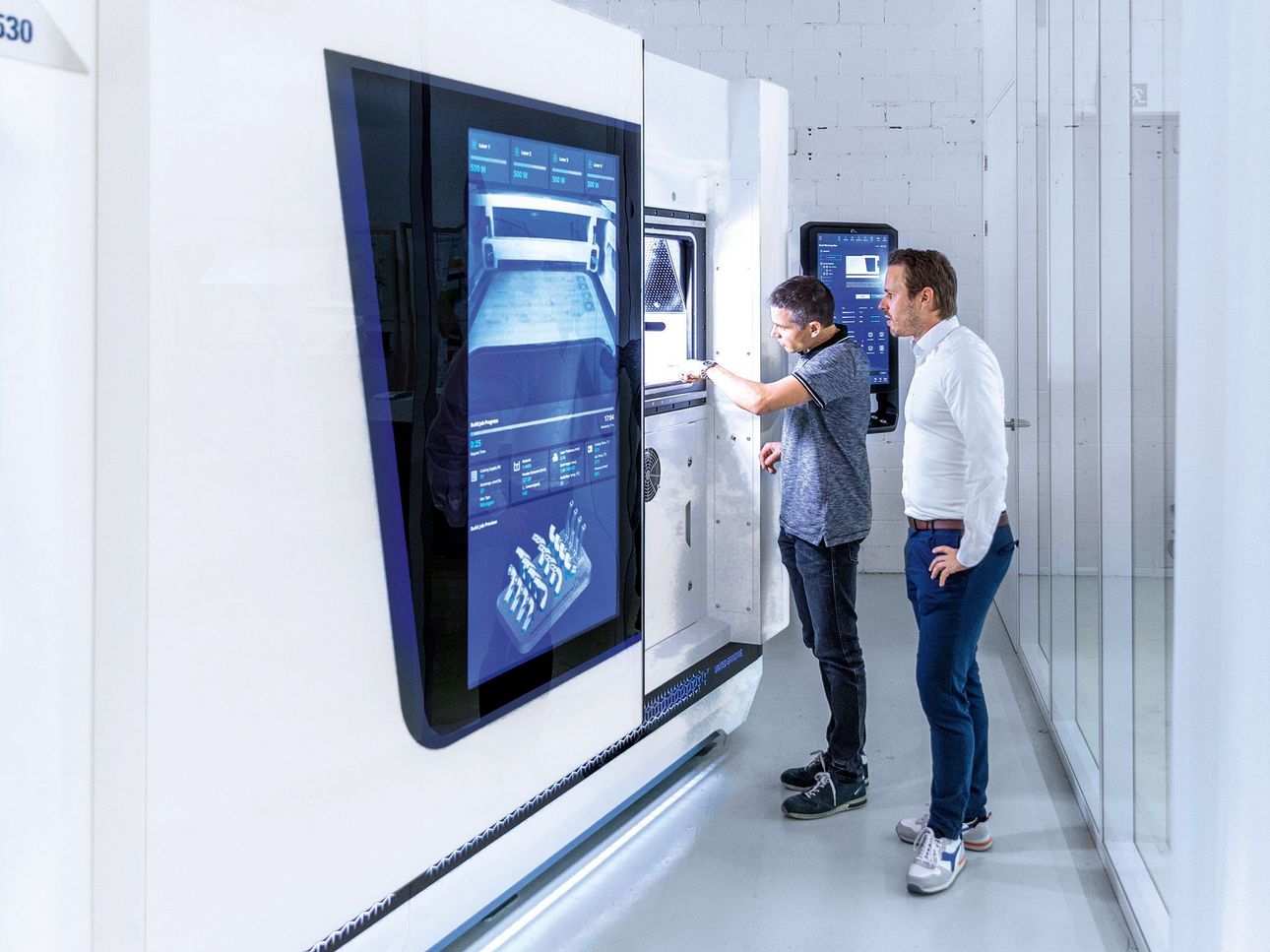
3D printing hedges against supply chain issues
Speed is an important factor, agrees Pascal Brunner, who is responsible for product development and IMPACT mechanics. “No tools need to be changed, no new blanks need to be clamped, and the machine doesn't needs to be adjusted for each job,” he says. All that's needed is the CAD 3D software file containing the relevant process data. By eliminating setup time, IMPACT can be warmed up in minutes and is highly flexible. Thanks to these advantages, it is suitable for the fast production of a large number of complex components, from single-unit batches to series production — for spare parts, standard production, and prototyping.
“The tailor-made component topology helps optimize a variety of processes and activities related to the different aspects of mechanical engineering,” explains material expert Frauchiger, “because the functionality of tools and components often depends on their surface.” Additive manufacturing can be used to manipulate properties in a targeted way, including corrosion and wear protection or sliding and lubricant behavior, adapting them seamlessly to customer requirements. The potential audience is huge and diverse: the classic job shop, automotive suppliers, or the aerospace industry.
Innovative atmosphere
How could so much innovation have possibly come from this team in the small town of St. Gallen? First of all, IRPD is no ordinary mechanical engineering company. Starting with its modular building on Lerchenfeldstraße featuring plenty of glass and style, the innovation and media hub is known as a “starting block” across the region. Machines stand here like polished exhibits, with a young engineer appearing now and again, a plexiglass visor over his face, to check on one thing or another. Its a contagiously good atmosphere, where everyone can feel like they are part of something big. The company’s origins in the nineties lie in an ambitious university project entitled “Institute for Rapid Product Development,” established at the Intercantonal Engineering School of St. Gallen (ISG), the university of applied sciences, and the ETH Zurich.
“Being able to experience the interplay between research and development up close and personal and tied to the provision of services, that's unique,” says Frauchiger. The team proudly shows the two predecessor models of the IMPACT 4530, a pair of machines still in use on a daily basis for the refinement of AM processes or for the production of components. The new 4530 is therefore the third generation of the machine, albeit one now capable of meeting the high demands of industry.
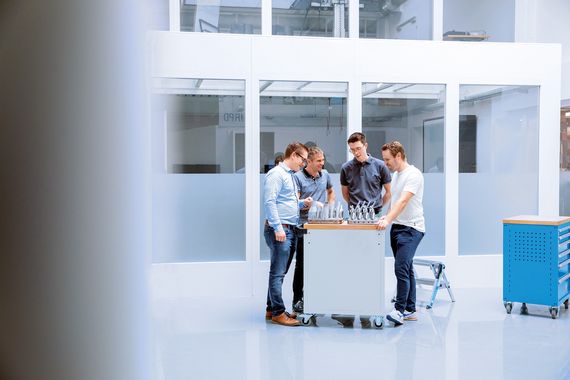
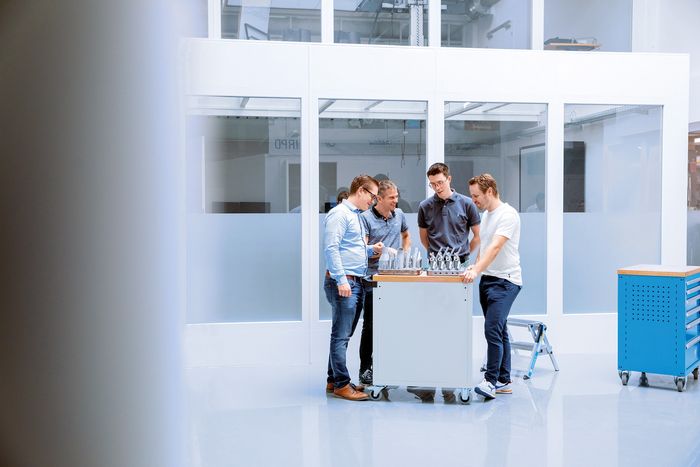
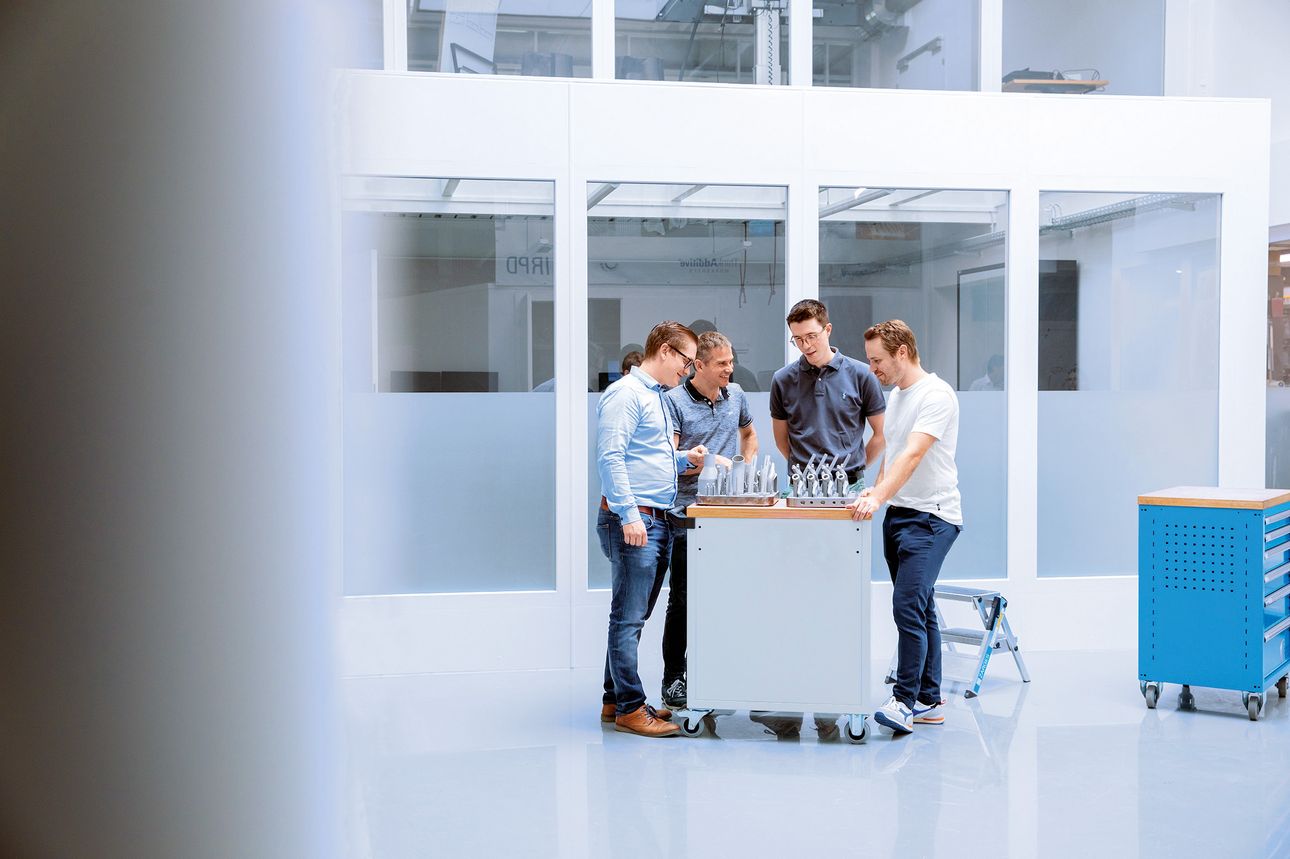
The spirit of St. Gallen
This university-style start-up spirit is one factor why one of the most innovative machine tools in the world was developed here in St. Gallen, just a few kilometers from the magnificent Baroque cathedral. The other reason is the integration into a leading international group of machine tool construction companies. The UNITED GRINDING Group has been the sole shareholder of IRPD since 2019, but enjoyed a long-standing cooperation long prior to that. “We can take advantage of synergies, and if we need support, we can find it, both in terms of expertise and capacity,” reports Michael Schneider. The IMPACT 4530 is being developed in St. Gallen, but is being built by its sister company STUDER in Thun, some 200 kilometers away. On the other hand, the sibling firms also benefit from additive manufacturing at IRPD. For example, the nozzles of the new SmartJet® cooling system are produced using the 3D printing process. Customers also benefit from synergies in terms of user-friendliness, networking, intelligent data processing, and automation: “The IMPACT 4530 comes with the C.O.R.E. hardware and software architecture, so it is compatible with all other brands in the Group,” explains Kai Gutknecht, who is responsible for software development. “The strong cooperation here in the team and with UNITED GRINDING,” he adds, “is the main reason why the IMPACT 4530 exists today.” There are nodding heads, smiling faces, and a good mood. “In the end, the customers benefit, which is the greatest success for us,” says Kössl and heads out from the “starting block” on Lerchenstraße, to the mountain landscape of St. Gallen, a place where a minor miracle has happened with the IMPACT 4530—one of teamwork, knowhow and the conviction that extraordinary things can be achieved with the right will.
Text: Michael Hopp, Photography: Thomas Eugster